HALT/HASS Space-age Technology Tested
HALT Based Design Process
The Ultimate Test for Reliability
The HALT test was initially conceived for testing electronic products for shuttle launch. The purpose of this test is to subject the product to a combination of high shock, vibrations, and a steep temperature gradient. MTBF of all electronic products depends upon the strength of connections of various components inside and HALT is the ultimate reliability test.
How it works:
1. Initial Design Specifications
Before a product is taken to the drawing board, all the desired specifications are laid out around which a product is to be designed. These specifications are based on the actual working parameters that are applied to our products in the industry. Let's pick an example of our Control Unit and see all the steps it goes through. The published specifications for Control Unit are to the right:
2. HALT Test of Finished Product
Once a product is designed and built as per initial specifications, it is subjected to HALT testing. Again, the point of this phase is to eliminate any pre-mature failure that might be present in its initial design. Based on the above published specifications, Control Unit is subjected to the following tests:
Without Power (Non-Operating)
A-Temperature Cycling: 20°C beyond published spec @ 100°C/min.
For Non-Operating (storage) conditions, the Control Unit goes through a total of 50 cycles of thermal shock in the range of -40˚C to +80˚C at the rate of 100˚C/min. If the Control Unit passes the Temperature Cycling test, it advances to next step. If for any reason the Control Unit does not complete the temperature cycling test for at least 50 cycles it goes back to drawing board for re-design and the process continues until it passes.
B-Shock and Vibration Cycling: 2 Times published spec.
After the Control Unit passes the Temperature Cycling test, it is subjected to Vibration and Shock testing as set by internal HALT specifications of 5-55 HZ 4 G’s for 2 hours maximum and 20 G’s for 12 ms respectively Non-Operating (storage) conditions. If the Control Unit passes the Shock and Vibration cycling test, it advances to the next step. If for any reason the Control Unit does not complete the Shock and Vibration cycling test for at least 50 cycles, it goes back to drawing board for re-design and the process continues until it passes.
C-Combined Temperature and Shock/Vibration: 20°C beyond & 2 Times Gs @ 100°C/min.
After the Control Unit passes the Shock and Vibration cycling test, it is subjected to a combined Temperature, Shock, and Vibration test as set by internal HALT specifications of -40˚C to +80˚C at the rate of 100˚C/min, 5-55 HZ 4 G’s for 2 hours maximum, and 20 G’s for 12 ms respectively for Non-Operating (storage) conditions.
Unit Under Power, Fully Functional (Non-Operating)
A-Temperature Cycling: 10°C beyond published spec @ 100°C/min.
For Operating conditions, the Control Unit goes through a total of 50 cycles of thermal shock in the range of -30˚C to +70˚C at the rate of 100˚C/min. If the Control Unit passes Temperature Cycling test, it advances to next step. If for any reason the Control Unit does not complete thetemperature cycling test for at least 50 cycles it goes back to drawing board for re-design and the process continues until it passes.
B-Shock and Vibration Cycling: 20% beyond published spec.
After the Control Unit passes Temperature Cycling test, it is subjected to Vibration and Shock testing as set by internal HALT specifications of 5-55 HZ 2.4 G’s for 2 hours maximum and 12 G’s for 12 ms respectively. If the Control Unit passes the Shock and Vibration cycling test, it advances to next step. If for any reason the Control Unit does not complete the Shock and Vibration cycling test for at least 50 cycles, it goes back to drawing board for re-design and the process continues until it passes.
C-Combined Temperature and Shock/Vibration: 10°C beyond & 20% beyond published Gs @ 100°C/min.
After the Control Unit passes the Shock and Vibration cycling test, it is subjected to a combined Temperature, Shock, and Vibration test as set by internal HALT specifications of -30˚C to +70˚C at the rate of 100˚C/min, 5-55 HZ 2.4 G’s for 2 hours maximum, and 12 G’s for 12 ms respectively for Operating conditions. After the successful completion of both Operating and Non-Operating HALT tests within specifications, the Control Unit is released for production.
HASS Based Manufacturing Process
HASS is an integral part of the manufacturing process at AVG/EZAutomation. The main purpose of HASS testing is to ensure that our manufacturing processes are in control. 1% AQL (per Mil Spec) level samples from the end of the manufacturing line are subjected to HASS testing to qualify and re-qualify the manufacturing process. If we detect a failure in HASS testing beyond acceptable Mil Spec numbers, the entire manufacturing lot is segregated for further screening.
The operating specification for the Control Unit is 0˚C to +45˚C with 2Gs of vibration and 10Gs of shock. 1% AQL sample of a production run will be subjected to HASS testing from -5˚C to +50˚C @ 2.2 Gs of vibration and 11 Gs of shock. Failure beyond Mil Spec number based on 1% AQL, will subject the entire lot to segregation and further analysis.
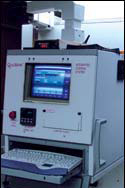
HASS Chamber
-60˚C to 150˚C at 100˚C/min @ 50 Gs of shock and vibration.
We invested over $500,000 in this HALT/HASS Chamber
Without Power (Non-Operating)
Unit Under Power, Fully Functional (Operating)